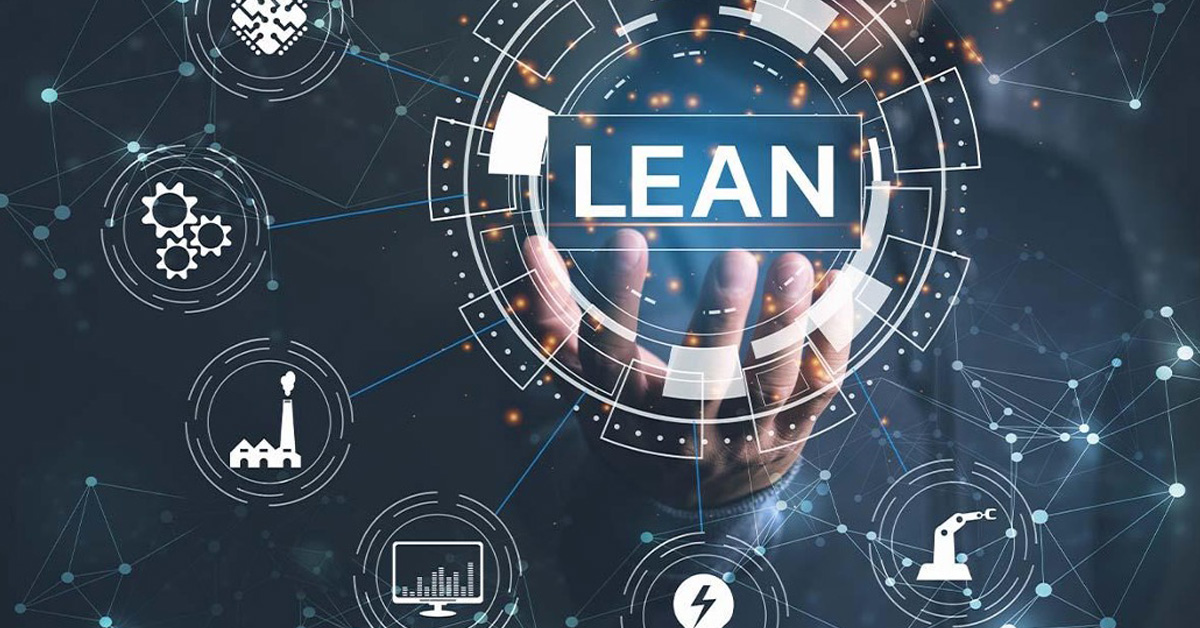
For decades, businesses have sought to develop or adopt various practices to optimise resources, boost profits, and build effective teams. Lean Six Sigma is a business management methodology that uses data and statistics to improve the efficiency of processes. According to Investopedia, its roots are in the U.S. manufacturing industry with the combination of Japanese management principles and techniques.
However, is Lean Six Sigma still relevant with the rise of newer methods such as Lean Startup and agile development? This article will explore what Lean Six Sigma is and discuss its applications, advantages, and disadvantages. We will then examine its current state and whether or not it is still a valuable tool for businesses.
Lean Six Sigma and how it works
Lean Six Sigma is an approach that aims to improve performance and quality through the elimination of waste and defects. It integrates Lean manufacturing techniques and the tenets of Six Sigma. In the 1980s, U.S. managers adopted Japanese manufacturing principles in a bid to compete with the latter’s high-quality products. At the time, Japanese manufacturers focused on minimising waste and doing away with non-value-adding activities.
Businesses use Six Sigma to eliminate defects and improve processes using a set of quality-control tools. It was introduced in 1986 by an engineer at Motorola and was inspired by the Kaizen model in Japan. In 1993, the company trademarked the term.
On the other hand, lean thinking is based on the principle of creating value using fewer resources and less waste. Toyota is often associated with lean manufacturing because of the game-changing innovations it made in the production process. The Lean Enterprise Institute reiterates that this methodology is not rigid and unchanging; rather, it develops in the “context of specific situations.”
Integrating the principles of Lean and Six Sigma, the main goal of Lean Six Sigma is to improve existing process problems. There are five phases taken from Six Sigma—DMAIC, which stands for Define, Measure, Analyse, Improve, and Control.
Go Lean Six Sigma provides a step-by-step guide on DMAIC. First, you need to identify and articulate what the problem is using tools such as a project charter or value stream map. Next, you need to quantify the problem to determine the current performance or baseline of the process. Here you need to formulate a plan on how to collect the data.
The third phase is getting to the root cause of the problem. By understanding the underlying issues, teams can avoid wasting time and resources in coming up with the wrong solutions. Instead, teams can develop hypotheses on why challenges arise and then work to prove or disprove them.
The fourth phase is about implementing and verifying the solution. This is the part where you can brainstorm and try out possible solutions. Remember, it is essential to collect data to confirm that there is measurable improvement. Lastly, teams must work to sustain the improvement by creating a monitoring plan to measure the gains and a response plan in the event of a dip in performance.
Lean Six Sigma beyond manufacturing
Despite its beginnings in manufacturing, the principles of Lean Six Sigma can benefit other industries as well. After all, the main focus is getting to the root of the problem, refining processes, and ultimately elevating the customer experience.
In healthcare, for example, instilling more efficient processes will help doctors, nurses, and other healthcare practitioners spend more time caring for patients. Likewise, streamlining administrative processes in schools will allow teachers to focus on students’ learning. Governments can also benefit from eliminating redundancies and wasted resources in order to provide better services to their citizens.
With the service industry being one of the hardest hit during the pandemic, businesses can use the principles of Lean Six Sigma to rethink how they can prepare for future challenges.
The Knowledge Academy also cites other sectors, such as logistics, biotechnology, entertainment, and the military, among others.
One of the main advantages of using Lean Six Sigma is that it allows companies to reduce costs and increase profits by addressing bottlenecks. Moreover, it encourages employee involvement through their participation in the process. Teams can develop a greater appreciation for the work that they do when they are given a voice.
Customer satisfaction is another benefit to consider. Lean Six Sigma does not only focus on product improvement but also on how the product or service is delivered to the customer. This can lead to repeat business and an overall positive brand image.
While there are many advantages to utilising Lean Six Sigma, there are also drawbacks. For one, it’s not a silver bullet, especially if you’re aiming for transformational change. Specific industries may not be ready to use this type of methodology. And depending on the issue, data-gathering and implementation can take some time.
Lean Six Sigma in today’s business environment
Lean Six Sigma has enjoyed industry-standard status for 35 years. And with the digital transformation of many industries, is it still relevant in today's business environment?
In increasingly competitive markets, businesses cannot afford to waste resources on activities that don’t bring in value. They must continually improve processes and working conditions to respond better to customers' needs. After all, the modern customer is more empowered than ever.
In this light, Lean Six Sigma is a data-driven approach that can help businesses succeed. However, it’s also vital to get the buy-in of your stakeholders and employees to be able to see the value of this hybrid methodology.
Regardless of the industry you’re in, every organisation needs to constantly improve the development of products and the delivery of services. Learn how you can enhance efficiency, productivity, and customer satisfaction with our Lean Six Sigma Green Belt Certification. Find out more about the course here.