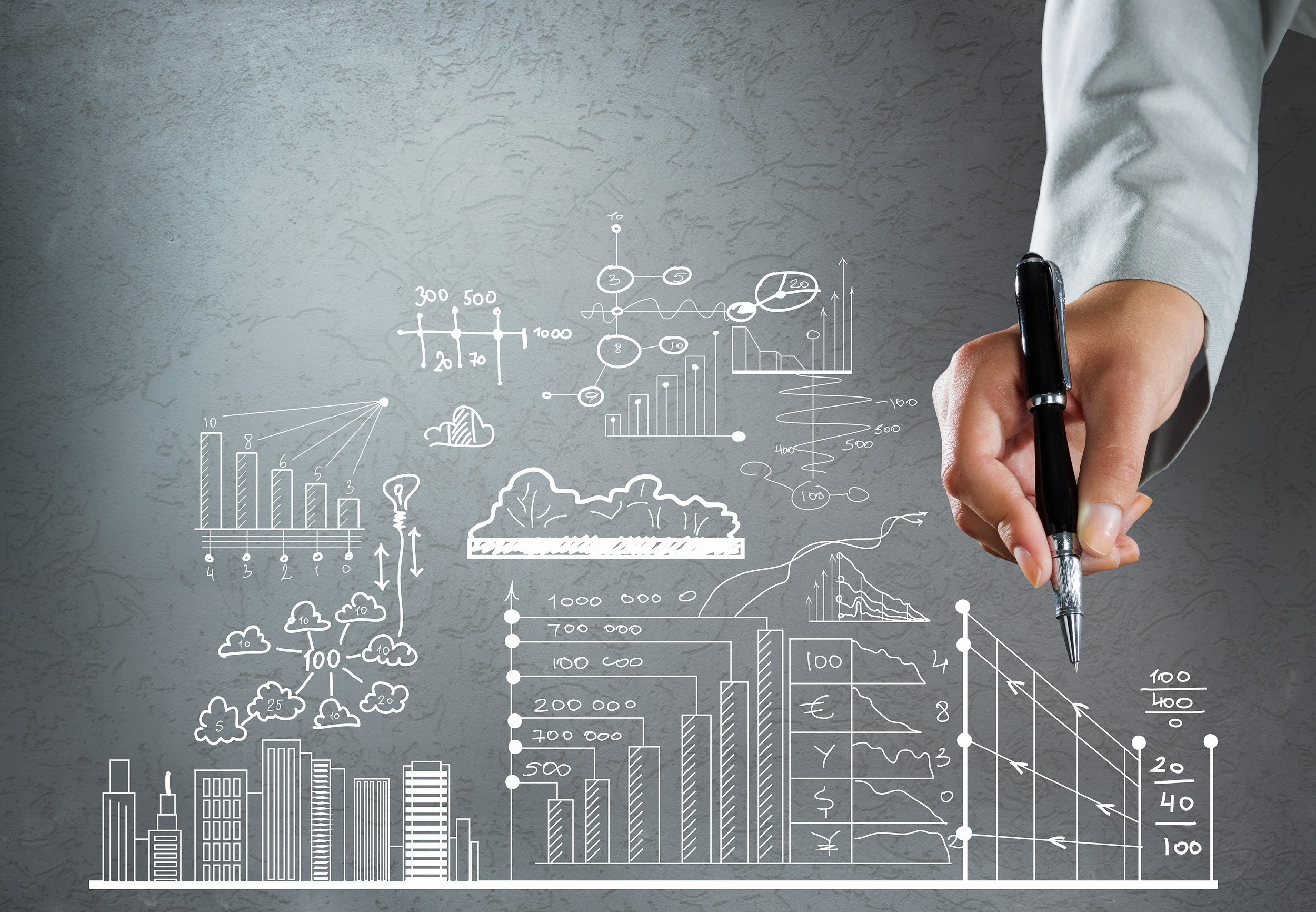
There is no such thing as a problem-free business. While that fact is a given, the way problems are dealt with differ between organisations with varying degrees of success. More often than not, it’s the successful, profitable organisations that are finding efficient ways of solving their problems not just temporarily, but definitively.
Lean Six Sigma (LSS) is all about efficient problem solving—about helping businesses of any size identify where they can streamline their processes, improve their products or services, and enhance their customer experience. This powerful methodology combines the Lean and Six Sigma schools of thought.
Lean focuses on the elimination of waste, while Six Sigma stresses working towards zero-error quality control. As Lean Six Sigma, both schools complement each other to result in greater efficiency in terms of processes and expenditure, as well as consistency in terms of production and output.
This is why major multinationals such as Boeing, Dell, Ford, General Electric and Amazon.com continue to apply and benefit from Lean Six Sigma principles, and put a premium on potential hires with Lean Six Sigma certification in Singapore.
By investing in the training of their own staff or looking for certification-holders to join their teams, these companies acknowledge how they stand to gain from those with LSS expertise.
With this in mind, LSS certification might be a prime consideration for you if you are dead-set on enhancing your career, regardless of what industry you happen to be in. Whether you are keen on joining a firm or growing one of your own, you’ll have much to gain by applying the Lean Six Sigma methodology on a personal or organisational level.
A Look at Lean
Lean helps organisations achieve efficiency by identifying and doing away with unnecessary parts of a business process, such as a step in a routine or excess packaging material that is just thrown away.
As obvious as that sounds, these unnecessary parts aren’t always as obvious to the people involved, and the necessary adjustments may take no little time or effort to make should they be pointed out.
To identify the fat that needs to be trimmed, so to speak, Lean poses this very simple question about a part of how a business provides its product or service: Would your customer be willing to pay for that? If the answer is “No”, then that part might have to go.
By implementing Lean, a business retains only the essentials, cutting down on production costs and saving a significant amount of time and other resources in the process. Work becomes faster, easier and far more productive for everyone involved.
Summarising Six Sigma
Where Lean helps to speed up and smooth out the production process, Six Sigma helps to reduce production errors—after all, there’s no point in providing a product or service more quickly or efficiently if it is defective or of substandard quality. Indeed, one way Six Sigma may be said to complement Lean is how it eliminates the need for revisions or reworking.
DMAIC stands for the five quality improvement phases in Six Sigma:
- Define the problems within a business process.
- Measure what can be quantified within the problem affecting the process.
- Analyse and shortlist the possible solutions to the problem.
- Improve the business process by implementing the best solutions.
- Control the outcomes of the implementations with constant output checks.
By implementing Six Sigma, a business produces significantly fewer defective products or provides much less, less-than-stellar service. Quality is boosted and remains consistent no matter who does the work, which means performance levels are less likely to be affected by staff changes.
A Powerful Combination
The beauty of Lean Six Sigma is that the customer is the focus of all its efforts. In other words, the ultimate reason for streamlining processes and improving quality is to provide a better product or service for the customer.
How the customer defines value is the driving force behind LSS—for Lean, anything that doesn’t add value for the customer is let go, and for Six Sigma, the inherent value of the business’ product or service is enhanced as much as possible. It is the value of your product or service—actual or perceived—-that your customer is paying for.
This means that in order to be truly effective, everyone in an organisation from the top brass to the intern that started yesterday needs to be truly service-oriented or customer-centric. In other words, everyone must commit to practising the Lean Six Sigma methodology.
This is where LSS specialists come in—to make sure that everyone understands what the methodology is, why it’s being implemented, and to oversee its implementation in every business process via projects or initiatives.
Leading with Lean Six Sigma
Achieving LSS certification goes a long way not just towards becoming that much more employable, but also towards becoming an invaluable asset to your organisation. The skills you acquire as you progress from Green to Black Belt levels will enable you to drive change within your business that will improve production processes and quality.
Thanks to your analytical abilities and your planning and implementation skills, you will be able to help your business to delight clients and keep them coming back as you build their trust and expand your customer base. The service you provide them will continue to improve as you continue to keep tabs on processes and make adjustments as needed.
You will likewise be instrumental in ensuring your organisation’s compliance with industry standards and regulations across economies, not to mention in saving it a lot of time, money and effort. You’ll also be playing a major role in helping your business to sustain healthy, profitable business relations.
On an individual level, working toward LSS certification develops your leadership skills as you hone your abilities in assessing risk and managing finances. This gives you an edge in landing a senior management position as well as above-average compensation, as companies are well aware of how hard it is to pass the certification exams.
Earning Your Belt
The Lean Six Sigma Green Belt Certification course at SMU Academy prepares you with a series of lectures, discussions, classroom exercises and projects. Ideal for aspiring and current managers, team leads, professionals and staff, the course also comes with coaching and assessments in the form of written tests and certification reviews.
For the heads of organisations and professionals, the Academy’s Lean Six Sigma Black Belt Certification course trains them to lead black belt level projects and to create a company culture of continuous improvement. SME owners will also learn best practices for building credibility via the delivery of superior business solutions and results.
Only Green Belters may apply for the LSS Black Belt course which comprises lectures, case studies, classroom discussions and activities, an online test, and the execution of an actual, LSS Black Belt-level project. Designed for busy executives, Black Belt sessions are limited to six inclusive of two nights and a Saturday.
The training is rigorous and the expectations are high, but the benefits to you and your organisation will continue to accrue long after you become a proud and accomplished LSS certification-holder. Besides, in today’s intensely competitive economic and employment environment, you and your business need every problem-solving advantage you can get.